Experience the Excellence
By seamlessly integrating proactive and reactive maintenance strategies into our operations, we ensure that the tools are always operating optimally. Combined with our extensive capabilities, including CNC machining and other advanced technologies, PLASTICUM maximizes tool performance and longevity, enabling us to provide consistent, high-quality injection-molded components to meet our clients’ exact specifications and industry demands.
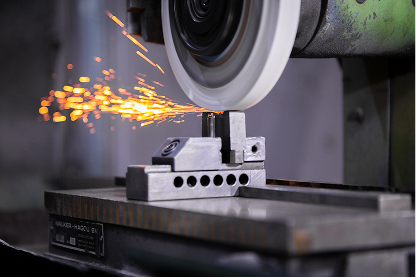
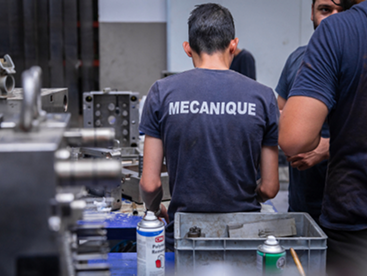
Empowering Plastic Transformation
The pursuit of precision is an ongoing journey. We constantly analyze data, gather insights, and make iterative refinements in our processes. These refinements are aimed at enhancing the precision of the tools, minimizing variability, and elevating the overall quality of injection-molded products.
Sculpting Innovation
Precision begins at the machining stage. We employ cutting-edge technologies, including CNC machining, EDM, and high-precision milling. These technologies enable us to craft tooling components with incredibly tight tolerances, achieving the exact specifications required for the injection molding process.
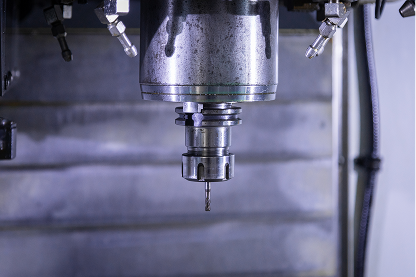
Crafting Dreams Together
At the heart of precision is excellent engineering. Our team of skilled engineers leverages their expertise and experience to meticulously design tooling that aligns with the project’s requirements. This includes assessing tolerances, material properties, and anticipated stress points to ensure the tool is designed for longevity and optimal performance.
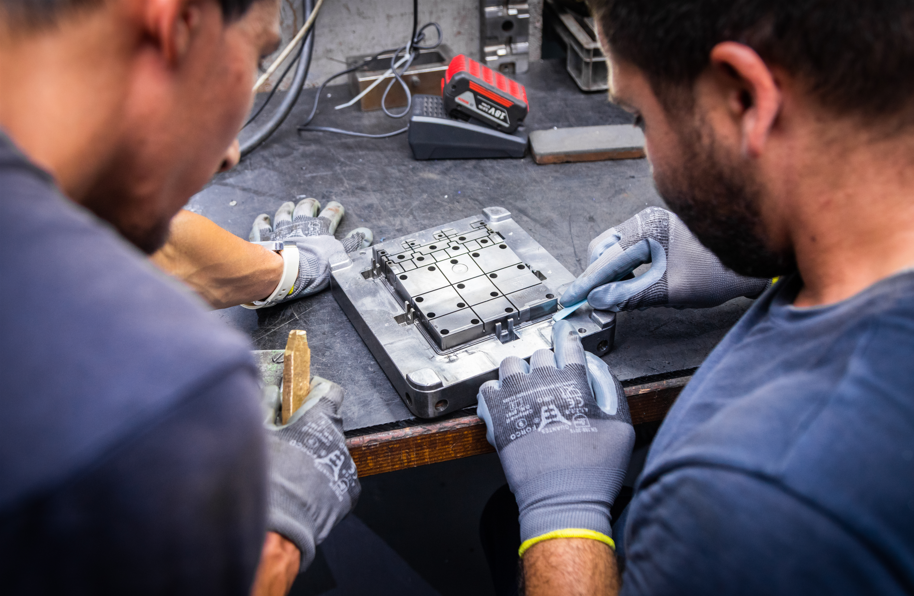
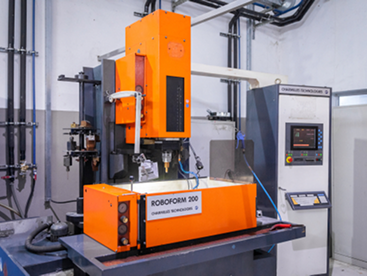
Industry-leading Tools
Our capabilities, including CNC machining, EDM (Electrical Discharge Machining), and advanced milling, are vital in tool maintenance and fabrication. CNC machining ensures precise and consistent tooling components. EDM is utilized for complex shapes and intricate details. Additionally, milling helps in tool modification and enhancement, contributing to extended tool life and improved performance.
Experience the Excellence
Our integrated tool management covers every stage — from design to maintenance — ensuring tool durability, production efficiency, and consistent quality.
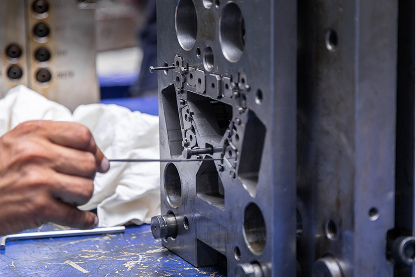
OUR TOOLING MANAGEMENT CAPABILITIES
BENEFITS
3-axis high-precision machining for mold base preparation and core/cavity work
Ideal for flat and moderately contoured surfaces
Supports hard steel and aluminum tool components
FEATURES
Reliable dimensional accuracy for mold parts
Enhances consistency in repetitive operations
Forms the foundation for robust, long-lasting molds
BENEFITS
Fine, non-contact welding for micro-repairs and modifications on tooling
High focus precision with minimal thermal distortion
Suitable for tight areas and complex geometries
FEATURES
Extends the life of expensive mold components
Reduces downtime during maintenance
Allows precise correction without disassembling the tool
BENEFITS
Electro-Discharge Machining for hard metals and fine tolerances
Wire cutting enables extremely precise cuts and internal features
No mechanical contact = stress-free machining
FEATURES
Enables complex shapes and undercuts that standard CNC can’t handle
Delivers tight tolerances essential for mold sealing surfaces
Increases tool quality, reducing cycle time issues in molding
BENEFITS
High-frequency sound waves to clean molds with precision
Reaches micro-cavities and tight mold sections
Uses non-abrasive cleaning liquid
FEATURES
Removes residue without damaging mold surfaces
Ensures consistent part quality by maintaining clean tool cavities
Extends mold service life with regular, gentle cleaning
BENEFITS
Dry ice blasting technology to clean molds without water or chemicals
Non-abrasive, non-conductive, and eco-friendly
Fast and safe for in-place cleaning
FEATURES
Minimizes mold maintenance time
No drying or reassembly needed = reduced downtime
Perfect for maintaining molds in production without heat distortion
BENEFITS
Enclosed cleaning unit (typically using filtration and airflow systems)
Designed to eliminate dust and airborne contaminants
Supports maintenance and inspection under controlled conditions
FEATURES
Protects critical mold components from contamination during handling
Maintains ISO-level cleanliness in tool preparation areas
Supports your quality assurance and traceability efforts
Applications & Grades
They are a base material in applications that do not require any formability beyond minimal bending and/or roll-forming.
- Large and Small Electric Motors
- Generators
- Ballasts
- Transformers